Slamfire, I'm interested to know if you plan to follow the "recommendations" on the Sarco webpage for these receivers. As in, square the receiver and bolt face, etc...
I have already checked out the lug engagement with Prussian blue. One of the split lugs is not bearing so some lapping needs to bring that into contact. Bearing was adequate on the lower lug.
Talked to the gunsmith, he is more concerned about even bearing on the inner collar than truing the receiver face. I asked him his opinion on truing the bolt face, he hemmed and hawed, he does not do it for himself, he trues bolt faces because everyone else asks for it. This guy is an active across the course and long range shooter. He has won the Long Range Matches at Camp Perry, he still shoots with a pre WW2 M70 that he did nothing to the action besides adding a new barrel and sight bases. (of course the trigger , stock, etc, have been changed to a target configuration) If he does not bother with this stuff target shooting, and is one of the top XTC and Long Range shooters in the US, I doubt it will make much of a difference on a hunting rifle. I will ask the gunsmith to check, but unless it is horribly off, I don’t want anything done. It is too easy for these guys to remove some of the bolt face shoulder when truing the bolt face. I do want all lugs to bear. The Mauser has split lugs on the left, if only one bears that might overstrain the bearing lug. Lug contact around 60% is fine, for me, on a new rifle. I am not a fan of lapping or grinding as there may be a case hardened surface and I don’t want it removed, and don’t like it being reduced in thickness. I am of the opinion that lapping, truing lugs, grinding, is something that is mandatory for major out of tolerance situations, but otherwise, as little as possible.
This M14 rifle bolt, it is on its third match barrel, all cases lubricated with Johnson paste wax, maybe it had 60-70% engagement when it was new. It has settled in nicely and the lug engagement has increased over time. I doubt I will ever get to a fourth barrel as I hardly ever shoot the thing anymore.
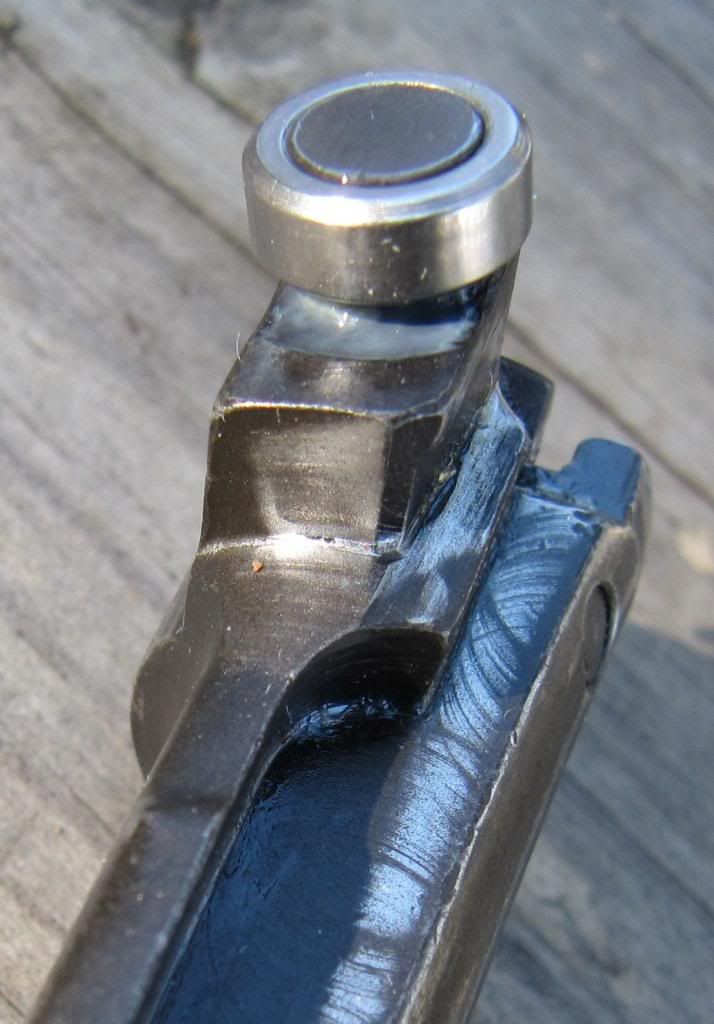
On my match Mauser, with a military receiver, I only asked for receiver face/inner collar truing, I have no idea how much the lugs bear in the receiver, but I shot hese 20 round groups, prone with a sling, with irons, in competition, with the thing, so I am not convinced that all that bench rest machining adds all that much in a hand held rifle.
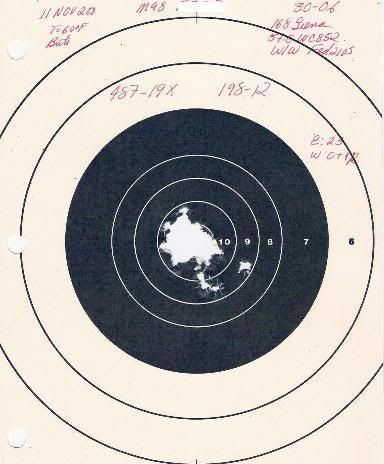
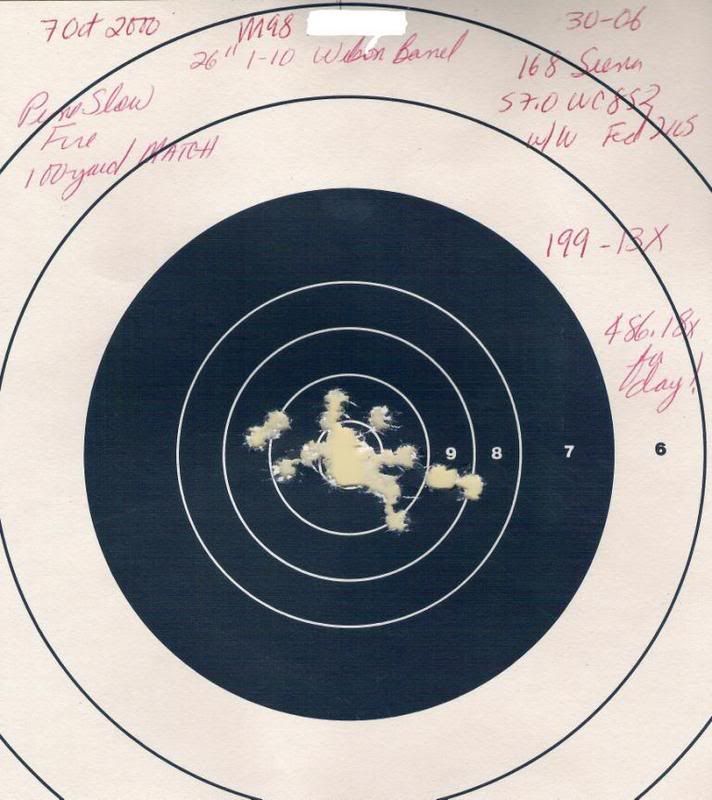
Last edited: