Yes, but also, manufacturers don't have to invest in the MIM equipment. Just buy the parts from somebody that has. This from my rarlier posted link.
Exactly. They spec the part they put it out to bid and award a contract. Not every process is brought in house.
Look at Pine Tree Castings, which is owned by Ruger, makes cast gun parts for tons of other companies.
http://www.ruger.com/casting/
When done right MIM is a solid way to manufacture a part. The same can be said of any manufacturing process.

The problem is when you get it wrong with MIM you get this ... http://thefiringline.com/forums/showthread.php?t=526661
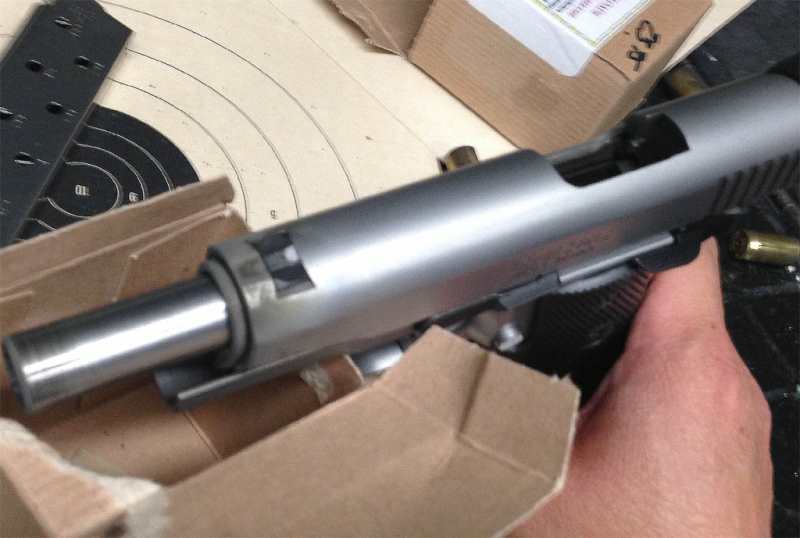