Kxkid,
A couple of things come to mind. First, Dillon dies are for progressive loading and because some brands, like R-P, often have thinner brass at the mouths that can become springy, in order not to produce some bad rounds during progressive loading, their sizing die rings are pretty much at minimum diameter. I used to just toss R-P brass in .45 Auto because they were so springy after a couple of load cycles, they'd come out of my Lyman carbide sizing die too wide to hang onto the bullet, which would just fall in. But after I got a Dillon Square Deal, the R-P didn't do that anymore because the Dillon carbide ring was a little narrower. So, I expect you have a pretty tight 9 mm sizing ring.
Second, the 9 mm, even more than the .45 Auto, has a tapered case, so when you push it up into a fixed diameter carbide sizing ring, it gets a good bit narrower near the base than is really required. This works the brass more than necessary, and because the brass case wall thickens lower down, you can find some bullets that reach the thicker brass when it is over-resized, squeezing the bullet base hard. If you are using any Dillon press other than the Square Deal (which uses proprietary dies with non-standard threads), then the you have a couple of options for getting around over-resizing. One way around this is to get a tapered steel 9 mm sizing die. That means lubricating cases, though. I had thought of the Redding Dual ring dies, but afterward looked at the catalog and see they don't make them for 9 mm; possibly it is too short to make that work well.
Another option is to get a Lee Carbide Factory Crimp Die and remove the crimp ring depth setting plug (just unscrews) and run all your cases through this die first, to ensure the bottom is withing case feed specs, then set your Dillon die up high in the press so it only resizes the case mouth as far as you feel you need to (experiment, but around 0.3 inches should work). The only problem with this is the Dillon die will no longer be decapping your cases, so you will want then to do decapping as a separate operation on a Lee Universal Decapping Die. By the time you've gone through that much extra effort (two additional dies and three steps) to resize, investment in the steel die will probably be looking more attractive.
The other thing you can do if you are using standard dies is, as suggested, get a Lyman M die or their Multi-expander die if you have other pistol chamberings you load for. These put a step in the case to keep the bullet upright, as shown below. That starts the bullets straight into the case, which is very helpful for keeping the bullet straight all through seating. My Square Deal 45 Auto rounds always have the bullet base mirrored in the surface, but because I turned my own powder drop tube giving it a Lyman M type profile, the mark no longer is ever on just one side of the case and pronounced, but rather is almost perfectly even all around the case and less pronounced because the bullet is seated straight.
A couple of things come to mind. First, Dillon dies are for progressive loading and because some brands, like R-P, often have thinner brass at the mouths that can become springy, in order not to produce some bad rounds during progressive loading, their sizing die rings are pretty much at minimum diameter. I used to just toss R-P brass in .45 Auto because they were so springy after a couple of load cycles, they'd come out of my Lyman carbide sizing die too wide to hang onto the bullet, which would just fall in. But after I got a Dillon Square Deal, the R-P didn't do that anymore because the Dillon carbide ring was a little narrower. So, I expect you have a pretty tight 9 mm sizing ring.
Second, the 9 mm, even more than the .45 Auto, has a tapered case, so when you push it up into a fixed diameter carbide sizing ring, it gets a good bit narrower near the base than is really required. This works the brass more than necessary, and because the brass case wall thickens lower down, you can find some bullets that reach the thicker brass when it is over-resized, squeezing the bullet base hard. If you are using any Dillon press other than the Square Deal (which uses proprietary dies with non-standard threads), then the you have a couple of options for getting around over-resizing. One way around this is to get a tapered steel 9 mm sizing die. That means lubricating cases, though. I had thought of the Redding Dual ring dies, but afterward looked at the catalog and see they don't make them for 9 mm; possibly it is too short to make that work well.
Another option is to get a Lee Carbide Factory Crimp Die and remove the crimp ring depth setting plug (just unscrews) and run all your cases through this die first, to ensure the bottom is withing case feed specs, then set your Dillon die up high in the press so it only resizes the case mouth as far as you feel you need to (experiment, but around 0.3 inches should work). The only problem with this is the Dillon die will no longer be decapping your cases, so you will want then to do decapping as a separate operation on a Lee Universal Decapping Die. By the time you've gone through that much extra effort (two additional dies and three steps) to resize, investment in the steel die will probably be looking more attractive.
The other thing you can do if you are using standard dies is, as suggested, get a Lyman M die or their Multi-expander die if you have other pistol chamberings you load for. These put a step in the case to keep the bullet upright, as shown below. That starts the bullets straight into the case, which is very helpful for keeping the bullet straight all through seating. My Square Deal 45 Auto rounds always have the bullet base mirrored in the surface, but because I turned my own powder drop tube giving it a Lyman M type profile, the mark no longer is ever on just one side of the case and pronounced, but rather is almost perfectly even all around the case and less pronounced because the bullet is seated straight.
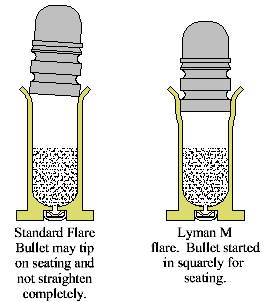