I don't have a problem reviving old threads, or updating them with knowledge gained since they were last written.
These old receivers have their own risks. Let me attempt to categorize some of the known issues.
It must be understood that between the wars, Government Arsenals were just as underfunded as the rest of the military. The parsimony of Congress, combined with a “kick the can down the road” attitude of military leadership meant that the Arsenals went through boom and bust cycles, with the bust cycles lasting decades. During the lean years, equipment became outdated, Arsenals would always be behind technological advancements. This is due to decisions made by Army leadership, no one else. However, Hatcher misdirects the blame on to the forge shop workers. This is from Hatcher’s Notebook.
The men though that they could tell when a piece had the right heat by looking into the furnace. They were proud of their experience, skill, and ability, and believed that it took years of practice to become expert in judging the forging temperature. They were highly paid craftsmen, who were jealous of their exclusive skill, and who both hated and feared these new fangled pyrometers which threatened to make useless their special knowledge
Let me throw out a couple of questions: Who was running this factory? Were the forge shop workers in charge of Springfield Armory? Did they decide the budget allocations? Did they have the budget authority to buy capital production equipment? Did they decide the production flow and processes? Just who was in charge of Springfield Armory?
Well it turns out, it was the Army who was in charge of Springfield Armory. If the workers had outdated production equipment, if the Arsenal had an out of control production flow, if the factory was shipping defective material, this is not the fault of the Forge Shop workers, it is due to the lack of management oversight and production insight by the appointed Army Army representatives who were in charge of Springfield Armory.
Hatcher uses a class envy stereotype to prejudice the reader against the forge shop workers. In this era of endless prosperity it is hard to understand the job insecurity created by technological advancements. (Sarcasm intended) However job obsolescence through technological advancements has always been an issue to workers ever since the beginning of the industrial revolution. It is not an issue to management as their costs go down when they reduce the number of people it takes to produce a product. However, back then, just as today, workers were being laid off because some machine did their job better and at less cost. Workers were not being asked their opinion in the matter, in fact workers have never been asked their opinion in this matter, management just goes down the path which brings the lowest cost.
Therefore the fears, opinions, attitudes of the forge shop workers are irrelevant and intentionally misleading. If Springfield Armory was producing defective product, it was the responsibility of Army Officers to provide the leadership to surface problems and fix them. I am of the opinion that what Army leadership was actually doing was playing Polo on the parade ground and between chukkers, drinking mint julips handed to them by their toadies and sycophants.
As for heat treatment, I have read Crossman, Sharpe, and others, and it is clear to me, all they know is heat treatment. They carp about heat treatment this and heat treatment that, but they are totally clueless as to the real problem in the Arsenals: lack of temperature instrumentation. Every time a metal part was exposed to heat there was no temperature gage to determine the temperature. Pyrometic cones go back to the 1780's, but there is no evidence that Springfield Armory was even using that simple temperature technology.
https://en.wikipedia.org/wiki/Pyrometric_cone Instead, Springfield Armory was using medieval process controls: human eyeballs. There is a short article in my 1914 Machinery Handbook about the unreliability of human eyes in determining steel temperatures, but I guess no one within the Ordnance Department paid any attention to that issue. It was inevitable that steel parts were being made brittle because humans can't accurately judge steel temperatures with their eyeballs. At least not within the forging temperature limits of the steels they used.
Currently there is an interesting program on the history channel:
Forged in Fire. Four knife/sword makers are given three hours to forge a knife blade from some blob of steel. It is worth watching this part, as even though the contestants are highly skilled, they forge by eyeball and there are a surprising number of burnt knife blanks created in the rush. The steel gets a little too hot, and the blade either breaks on the anvil, or there are visible cracks in the blade. I saw one episode where the tester refused to test one blade with multiple cracks as it was highly likely the blade would fail and the tester would be injured in the test. I have seen a number of episodes where knives that looked OK proved to be too brittle by losing big half moon chunks out of the edge during a chopping test, or the blade simply breaks. Of course the tape is moved in slow motion when a blade breaks and there is the sound effect of a something heavy falling. Quite entertaining, and instructive as it turns out, to this debate.
Production technology was moving so fast, that this Jan 1926 book review, from the
Transactions of the American Society for Steel Treating, is germane to the issue of forging, and the process controls for forge temperatures.
Making Springs for Motor Vehicles
Canadian Machinery, 12 Nov 1925, page 15
The author of this paper discusses the benefits that have come to the manufacture of springs in the motor car industry from metallurgical research. Springs today stand four or five times the work of those a few year ago because the “skill” and “guessing” of the forger has been replaced by heat treating furnaces with temperatures maintained at the proper degree by pyrometers. The Dowsley Spring and Axle Co., Chatham, Ont., a subsidiary of the Ontario Products Co., is taken as an example of a thoroughly modern plant, and its work discussed. There are 145 men employed in the plant and production averages about 55 tons of springs a day, a single spring weighing anywhere from 17 to 44 pounds.
The plant is so arranged that material follows a straight path from storage to shipping room. Until a few years ago all springs were heat treated in small oil-fired furnaces. Today this method had been discarded. A continuous heat treating, forming, and quenching process has been evolved, which is practically automatic and eliminates the human element. As an example of what careful- heat treatment has done toward prolonging the life of springs, the results of test of springs made by the hand method and those by the continuous heat treatment method are interesting. Some years ago 40,000 deflections were about the average before failure, now 120,000 is a low figure.
(If anyone has the complete Canadian Machinery article I would be grateful to get an electronic copy)
So the first and foremost risk associated with low number receivers is a lack of material property consistency due to non existing temperature controls. A burnt billet of steel cannot be improved through heat treatment or any process. Burnt is burnt. Steels forged and heat treated as inconsistently as the low number Springfield’s are going to vary widely in hardness and structural integrity. As Hatcher says, in Hatcher’s Notebook page 222:
In one of the experiments at Springfield Armory, 48 receivers were carefully re-heat treated, after which 16, or one-third, failed on high pressure test. Some people may consider a 33 1/3% failure rate acceptable, but I don't think so.
Another issue with these old receivers is the single heat treatment as practiced by Springfield Armory was just a heat and a quench, which is actually a very poor heat treatment. Even period books, my first edition Machinery’s Handbook shows they should have done a heat, quench, and temper, to relive stresses. As primitive the heat treatment of these early receivers, so was the process technology at the steel factories that produced the plain carbon steels used in these rifles. People without a historical understanding of technology just don’t know how little the people back then knew, and how primitive the process controls of the period. Primary instrumentation was often a human’s sense of sight, smell, taste, touch. The end result was that the steels of that period had a lot of slag and impurities. The exact same steel made today would be cleaner and have better material properties. And these same steels are being made today, and used as rebar, or rail road ties, applications that are not high stress and where ultra low cost is the most desired property.
The plain carbon steels used in the single heat treat and double heat treat receivers were technologically obsolescent in 1918. If you remember, the British used nickle steel in the P1914, and so did we in the P1917 rifle. In a few short years plain carbon steels were being replaced with alloy steels for a number of very good reasons. Metal technology advanced quickly in the first and second decade of the 20 century, and even more rapidly after 1920. Maybe steel technology moved as rapidly as did the transistor revolution from the 1960’s to the end of the millennium. I listened to vacuum tube radios and I remember the “6 transistor” radios of the early 1960’s. Dick Tracey had a mobile phone on his wrist, but he was a comic book character and I was listening to a crystal radio at the time.
Post WW1 it was painfully obvious that the use of plain carbon steels in safety critical or stressing environments was not technically justifiable. The American metallurgist Edgar Bain,
http://www.nasonline.org/publications/biographical-memoirs/memoir-pdfs/bain-edgar-c.pdf in 1932 published conclusive experiments on carbons steels. Bain heat treated identical plain carbon steel coupons under identical conditions and examined the coupons afterwards for hardness depth. The black chemical etching, which I assume is the unhardened steel, show that plain carbon steels have erratic hardening depths, given that all else is equal. These steels were called in WW2 era text books as
“shallow hardening”. This was meant not as praise but as a pejorative. As is shown on the right of the diagram, the hardness of these coupons varies by depth. This is not good as inconsistent hardening depths provide inconsistent material properties. It is undesirable to create parts some of which will be hard through and through but others soft below the surface even though the heating processes are the same for all parts. But use plain carbon steels, and you will create such inconsistent parts, just by the nature of the material.
Therefore, you would expect even properly forged, properly heat treated single heat treat and double heat treat receivers to vary considerable in hardness depth, which then affects the properties of the end part.
Yield is an extremely important material property, for above yield, the part deforms. Once a steel part yields it is no longer safe to use. What happens after yield is unpredictable, often it takes less load to cause more deformation, ultimate load is the load it takes to break the part. In this early 1920’s chart, for the same essential heat treatment, the nickel alloy steel always has a higher yield, a significantly higher yield in all cases, than the plain carbon steel. I am of the opinion that the 3.5% nickle steel in this chart is 2340, which is the nickle steel used in the nickle steel 03's.
Nickel steel versus plain carbon steel
What is not shown in these charts is a material property called toughness. For a device, such as a receiver, which is going to be subjected to impact loading, toughness is a highly desirable property. Toughness is directly related to fatigue lifetime, which is the number of loading cycles to failure. Assuming the yield is sufficient for the load, the tougher material will have a longer service life. Alloy steels have a greater toughness than plain carbon steels. Alloy steels take more energy to shear, Charpy impact tests are a direct predictor of a steel’s fatigue lifetime. It is a revelation to see just how shear energy decreases with temperature, and at low temperature, alloy steels take several times the energy to shear as do plain carbon steels.
Therefore, old single heat treat receivers are a very significant unknown quantity. We know they were made in a factory that did not have temperature controls, we know that the material varies considerably in properties after heat treatment, and that the service life of the part will always be less to one made out of a good alloy steel. Just how many service lives have these old receivers been though? How many more load cycles will they take before failure? How will they react in an overpressure situation?
Therefore, regardless of the hoopla around double heat treat receivers, or “old world craftsmanship” these old plain carbon steels are inferior in all aspects to alloy steels. As a class, low number receivers have a number of identified risks. The process control technology they were made under produced a number of structurally deficient parts, and a number of people were severely injured when their rifles blew up. The steels of the era were inconsistent in composition and inherently inconsistent in final properties after heat treatment. Also, these steels were rather primitive, by WW2, called low grade, due to their lack of strength and ductility. All of these receivers have been around a long time. Some have been through a number of service lives, at some point they will fail through structural fatigue, just when, I don’t know.
However assessing risk on a large population is a lot easier than assessing risk on an individual receiver. I am not going to say, sight unseen, and untested, that any low number receiver is safe or defective. I can’t. But I can say, as a population, there is a lot of risk in the group.
A simple test of a low number receiver, to determine brittleness, is to do what the Marine Corp did. Take the action out of the stock, take the bolt out, and hit it sharply with a heavy steel hammer a number of times. Make it ring, make it ring loudly. Whack it on the receiver ring, the right rail, and the rear bridge. If it shatters, you had a defective low number receiver, and you saved yourself from potential injury.
This low number came cracked from the CMP
I don't remember why this low number came apart.
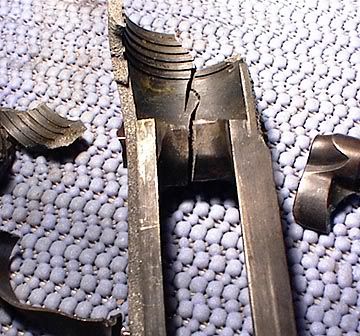