Hi guys.
I need help, I am trying to get into reloading and have everything. Im working on a Hornady LnL AP and I got a set of match grade dies for the .223 along with the correct bushing for the FL sizing die. So right now im getting my sizing die set up. So I followed Hornady's instructions to screw down my sizing die till it makes contact with the shellplate and locked it down . I have some once fired LC brass that i bought already cleaned, swaged and deprimed, so I case lubed as directed and resized a couple. After resizing some I used my lyman case gauge and the casehead sticks out further that the max headspace allowed. :/ I tried Lowering my Sizing die as much as I could but still does not fix the headspace.
Am I doing something wrong?
Could it be the brass I bought??
What should I do.?
I attached some pictures so you can see how far is my sizing die and how far my brass sticks out.
Any help would be appreciated.
Andres
I need help, I am trying to get into reloading and have everything. Im working on a Hornady LnL AP and I got a set of match grade dies for the .223 along with the correct bushing for the FL sizing die. So right now im getting my sizing die set up. So I followed Hornady's instructions to screw down my sizing die till it makes contact with the shellplate and locked it down . I have some once fired LC brass that i bought already cleaned, swaged and deprimed, so I case lubed as directed and resized a couple. After resizing some I used my lyman case gauge and the casehead sticks out further that the max headspace allowed. :/ I tried Lowering my Sizing die as much as I could but still does not fix the headspace.
Am I doing something wrong?
Could it be the brass I bought??
What should I do.?
I attached some pictures so you can see how far is my sizing die and how far my brass sticks out.
Any help would be appreciated.
Andres
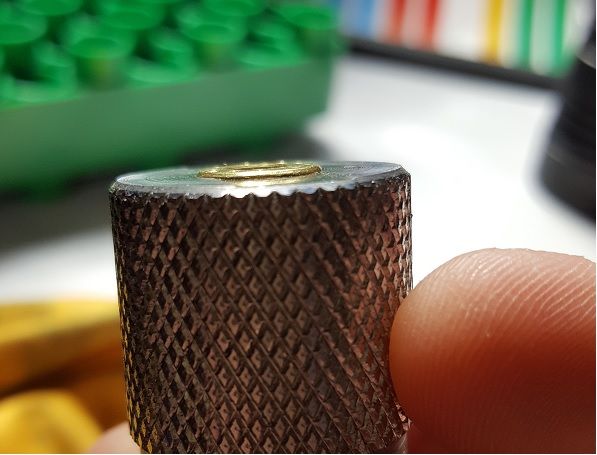
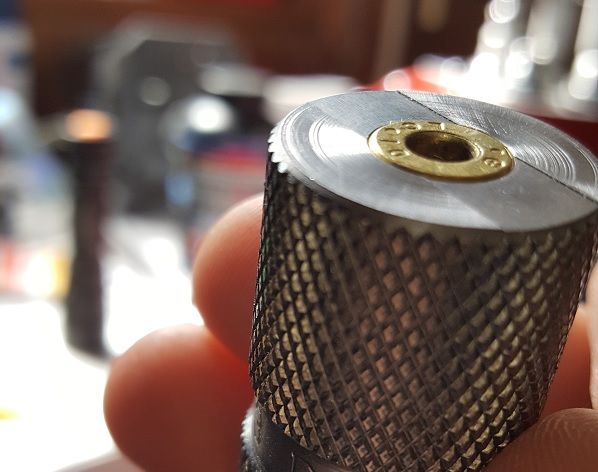
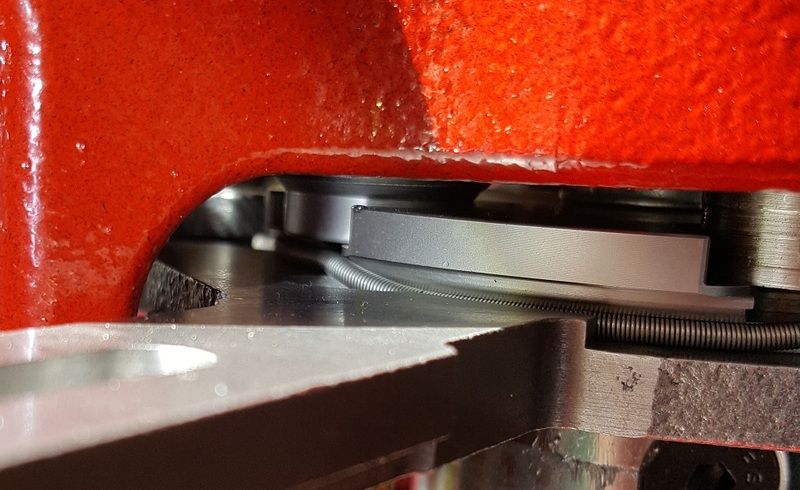