Dixie Gunsmithing
Moderator Emeritus
I just finished my new polishing buffer project, and thought I would show some photos of it. It uses a 1/2 HP, reversible, capacitor start motor, running at 3500 RPM. The motor speed is reduced to 1750 RPM at the wheels, via a 2:1 chain reduction system, supplying approximately the same running torque of a 1 HP motor. As shown, it uses two 8" wheels, but could use 10" easily. The wheels run on a 3/4" drive shaft, and the wheel centers are 36" between. The arbors are 1/2-20 standard thread. I also have a sanding drum, and a drill chuck arbor, for the right hand arbor to use.
Baldor, eat your heart out!
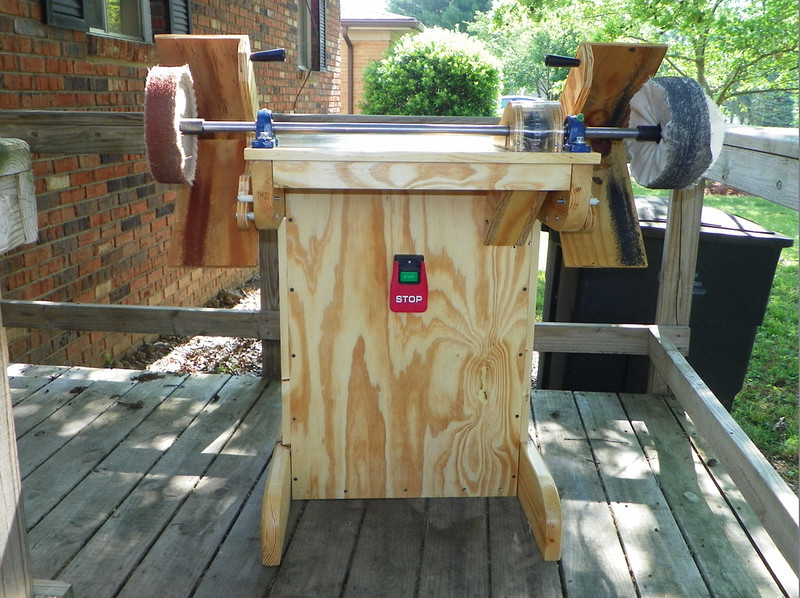
2013-05-29_114047 by matneyw, on Flickr

2013-05-29_114028 by matneyw, on Flickr
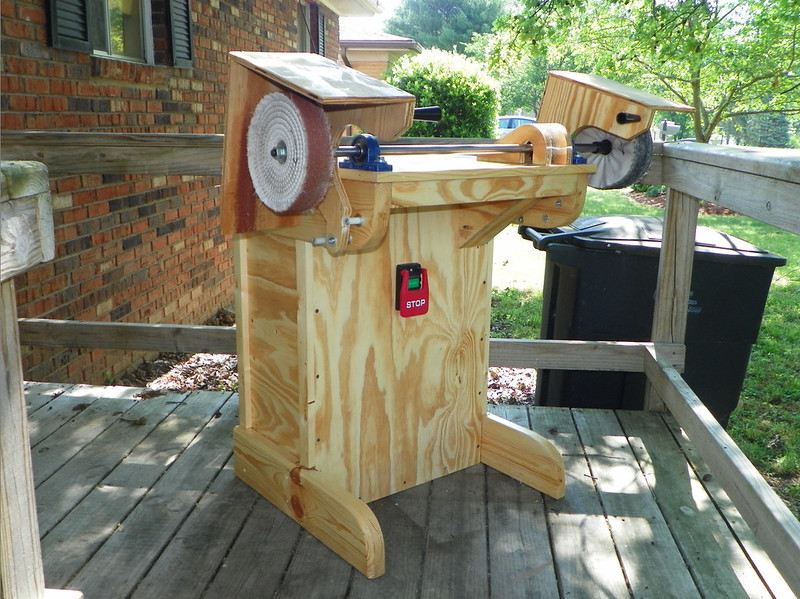
2013-05-29_114118 by matneyw, on Flickr

2013-05-29_114209 by matneyw, on Flickr
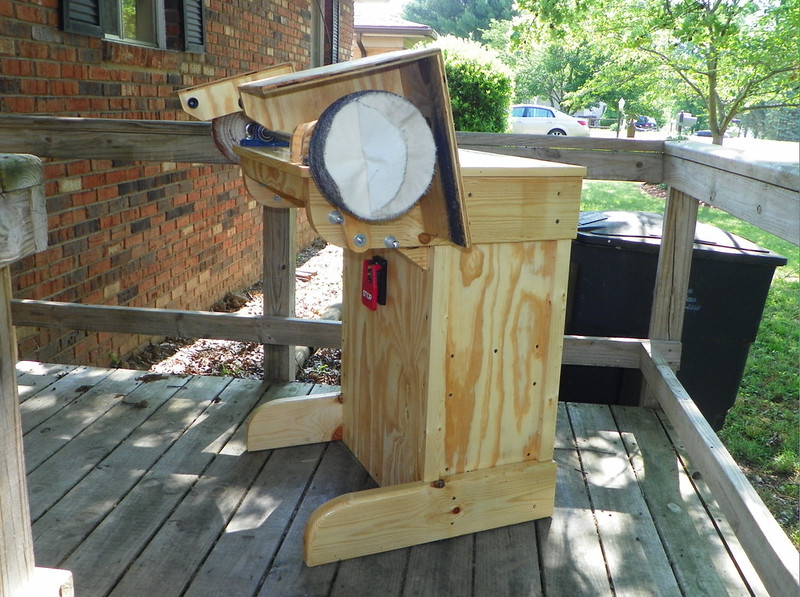
2013-05-29_114153 by matneyw, on Flickr
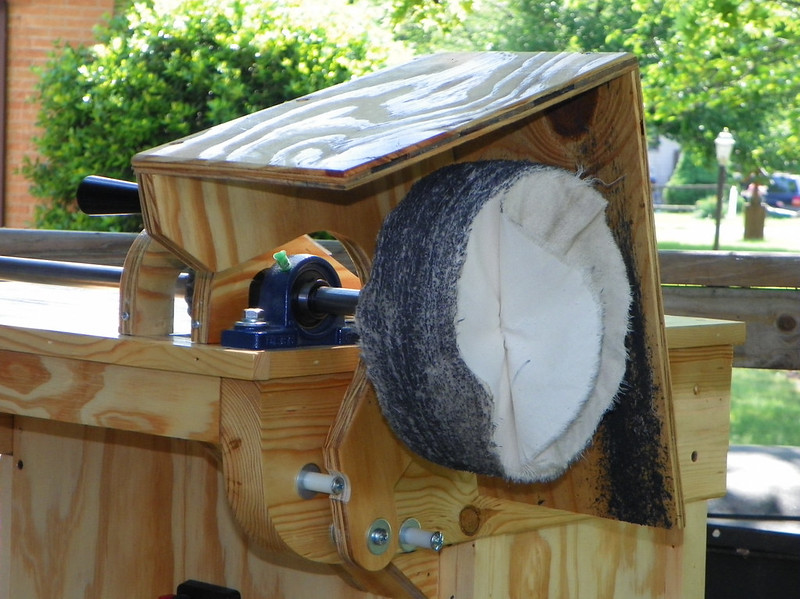
2013-05-29_114009 by matneyw, on Flickr
Baldor, eat your heart out!
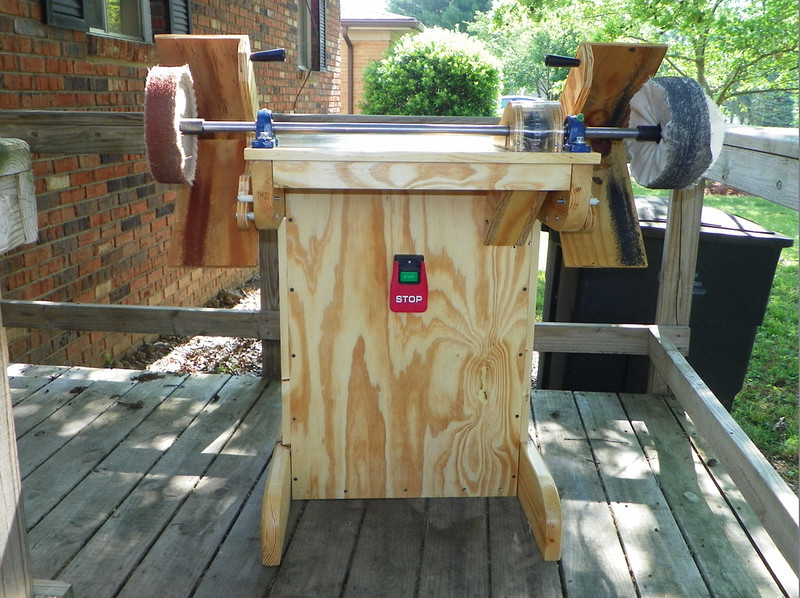
2013-05-29_114047 by matneyw, on Flickr

2013-05-29_114028 by matneyw, on Flickr
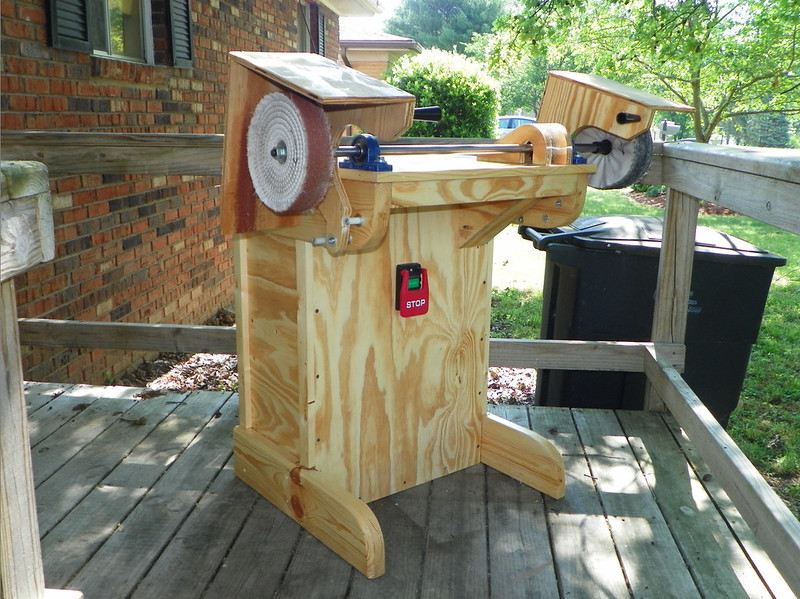
2013-05-29_114118 by matneyw, on Flickr

2013-05-29_114209 by matneyw, on Flickr
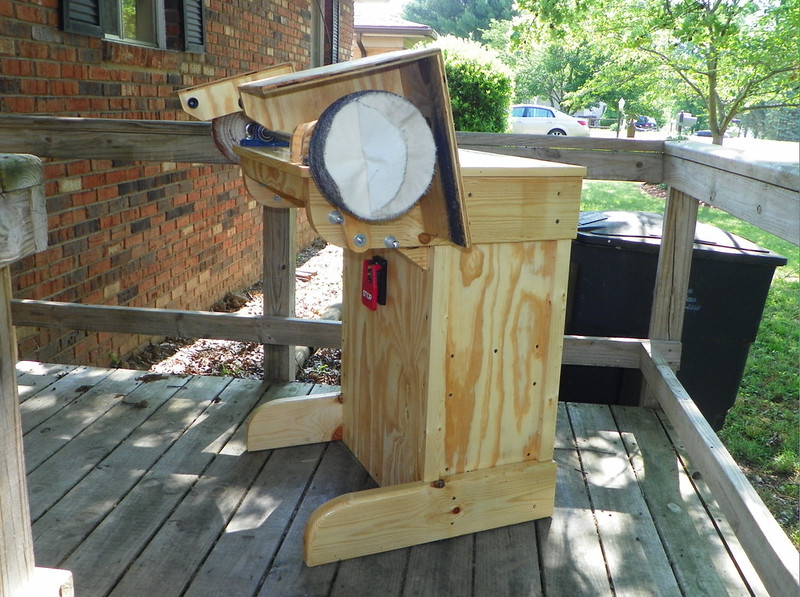
2013-05-29_114153 by matneyw, on Flickr
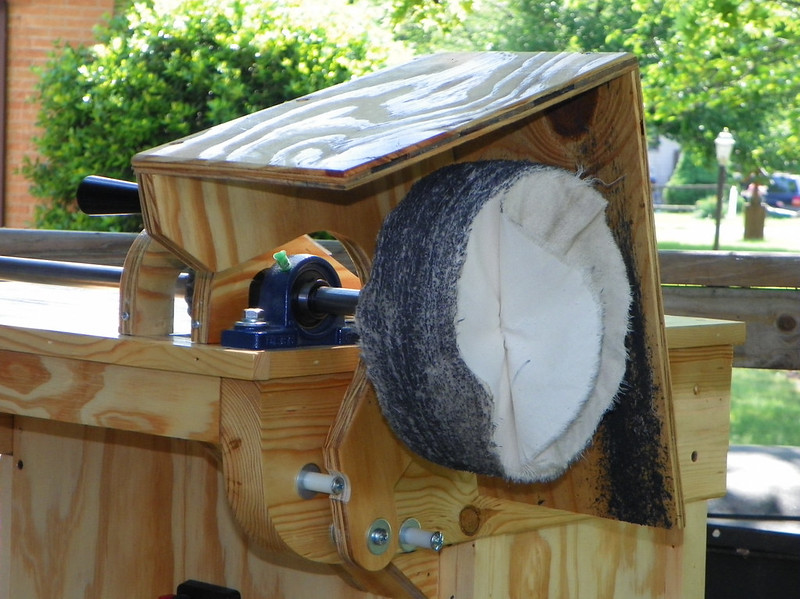
2013-05-29_114009 by matneyw, on Flickr