Has anybody got any experience with these? Supposedly, you cast a pure lead nose section and then you cast the body out of wheel weight or harder and then you can epoxy/glue or whatever the ultra-soft nose section down into the body of the SWC bullet. I'm thinking powdercoat would hold it down in there quite nicely.
Yes, it'll be slow. Yes, it'll be slightly aggravating. But I just wanted to play a little while with this piece of history and then I'll probably sell it off when the new wears off. But as of now, it's new and uncast and just waiting for me to have time to get out to the casting shed.
Yes, it'll be slow. Yes, it'll be slightly aggravating. But I just wanted to play a little while with this piece of history and then I'll probably sell it off when the new wears off. But as of now, it's new and uncast and just waiting for me to have time to get out to the casting shed.
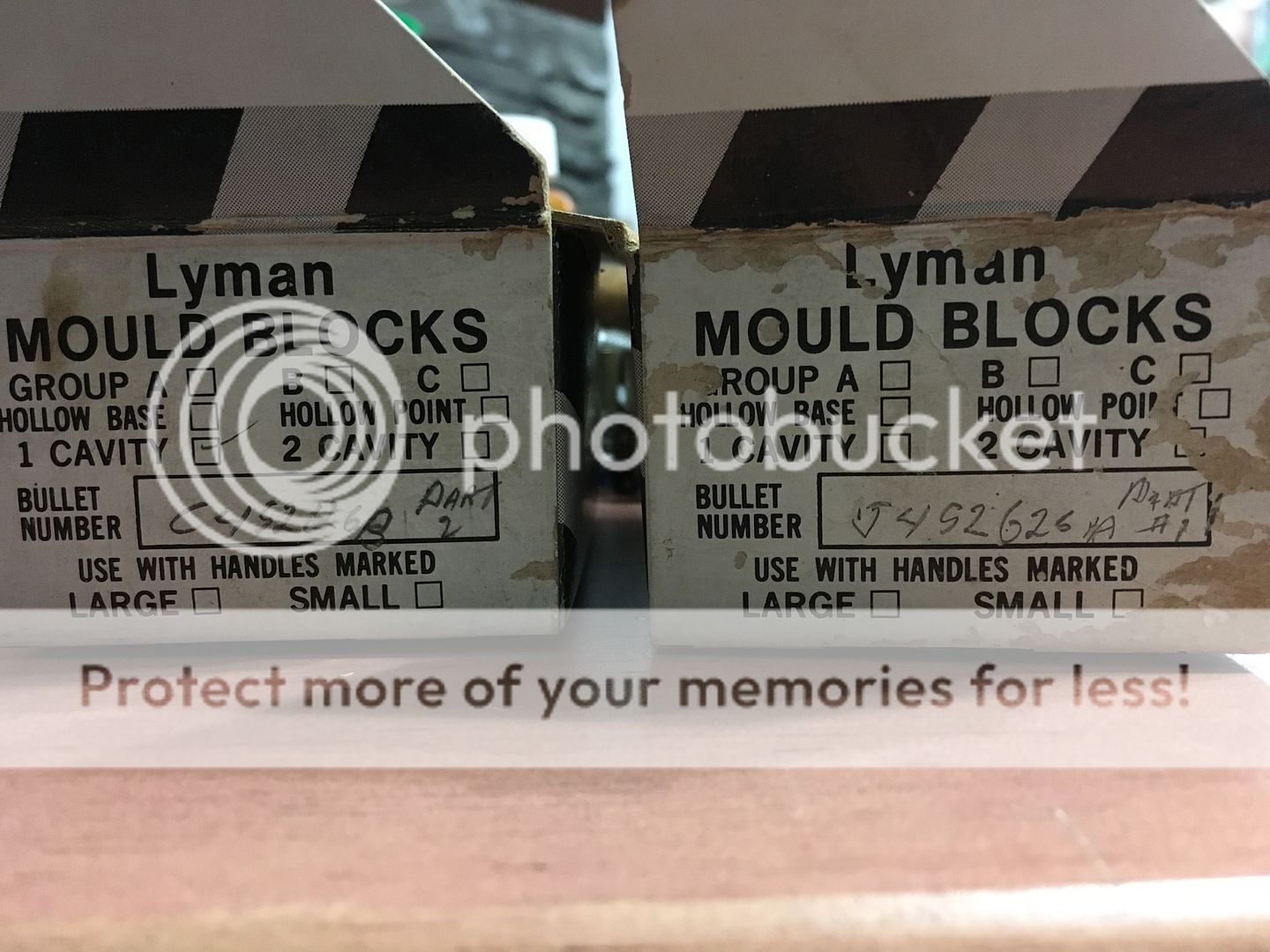
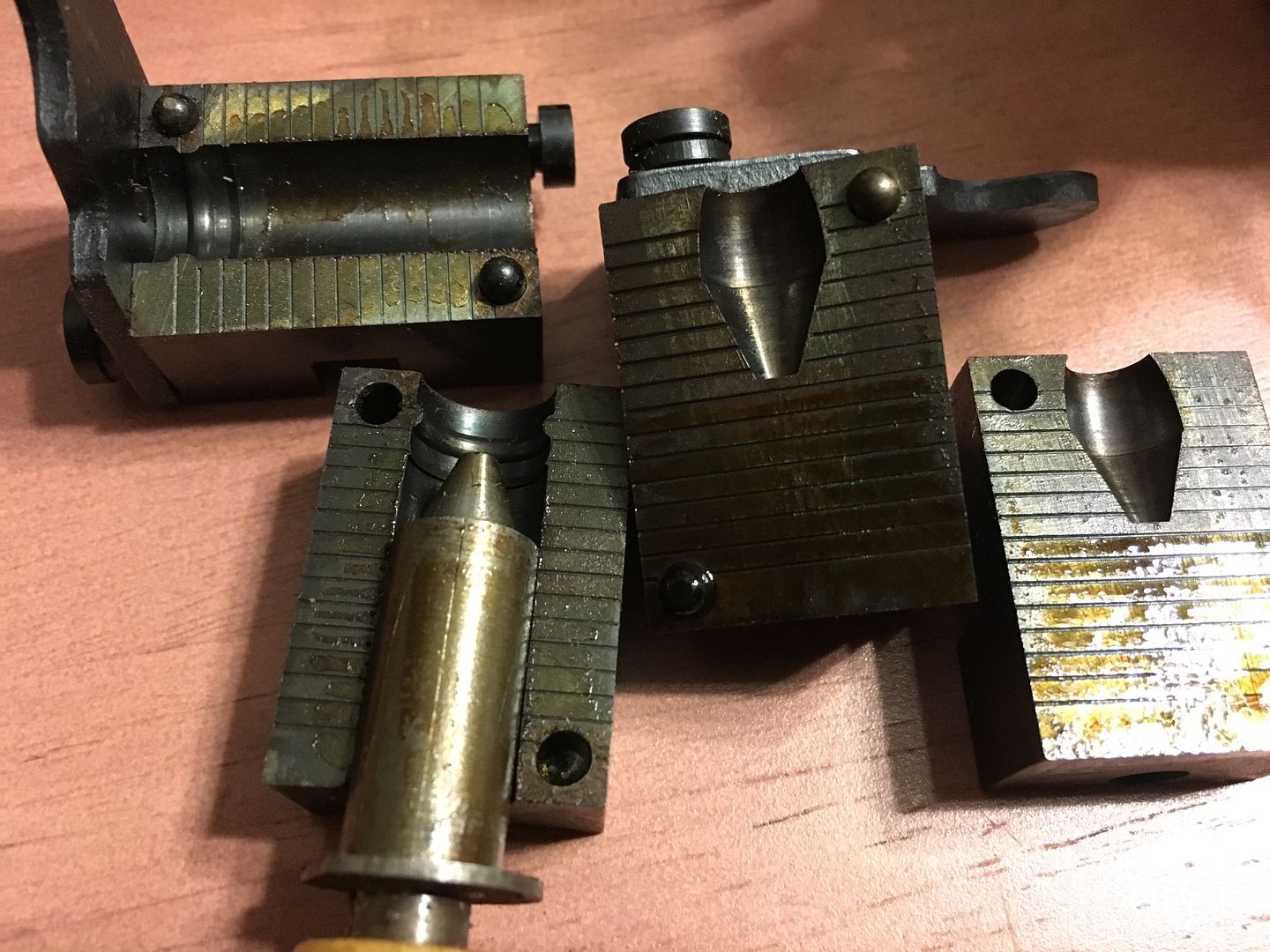