I just cast my first bullets, and I think I have some slight issues. About 40% of the bullets I cast have some kind of wrinkles in the nose, as shown in the first photo below. Is this due to the lead not being hot enough? The other 60% looks good and smooth. The second issue is that all of the bullets, even the ones that look good, have a round mark from where the sprue plate hole is. Since the base is important for accuracy, I'm guessing this could be a problem. I am using a Lee 2 cavity mold casting straight wheel weights and quenching the bullets to harden. I know wheel weights already have some tin, but perhaps I need to add more?
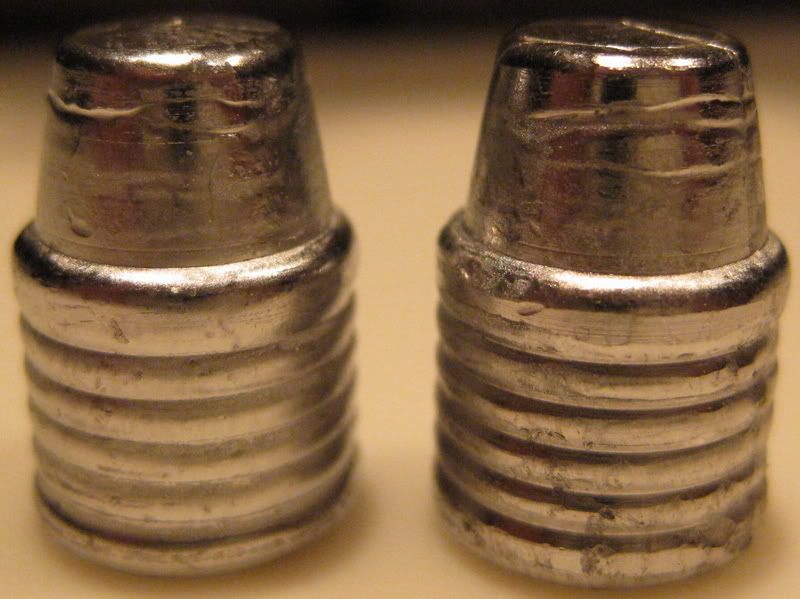
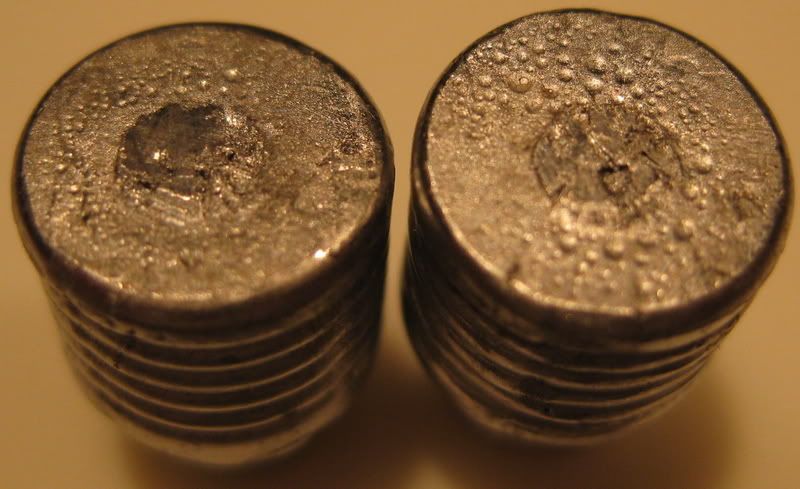