A pause for the COZ
New member
When I first started casting, the hardest part to figure out was getting proper mold temp.
Spent allot of time tweeking my melt try to get rid of the waves out of my bullets.
Turns out 80% of casting problems are related to mold temp. Well at least they were for me.
Found a fool proof way ( I know I qualify) to insure my molds and melt are ready at the same time.
If you have not done it yet, grab your self a cheap hot plate off Ebay, Hardware store where Ever. I added a old saw blade to give a even surface for the molds to sit on.
When I get ready to cast. I set the molds I plan to use that day on the hot plate, Put my ingots into the pot. Plug them both in and go do some thing else for 30 minutes.
When I come back, Throw some saw dust in the pot to clean up the melt.
Bam!!! Start casting. Very rare if I do not get lube ready bullets on the first drop.
Spent allot of time tweeking my melt try to get rid of the waves out of my bullets.
Turns out 80% of casting problems are related to mold temp. Well at least they were for me.
Found a fool proof way ( I know I qualify) to insure my molds and melt are ready at the same time.
If you have not done it yet, grab your self a cheap hot plate off Ebay, Hardware store where Ever. I added a old saw blade to give a even surface for the molds to sit on.
When I get ready to cast. I set the molds I plan to use that day on the hot plate, Put my ingots into the pot. Plug them both in and go do some thing else for 30 minutes.
When I come back, Throw some saw dust in the pot to clean up the melt.
Bam!!! Start casting. Very rare if I do not get lube ready bullets on the first drop.
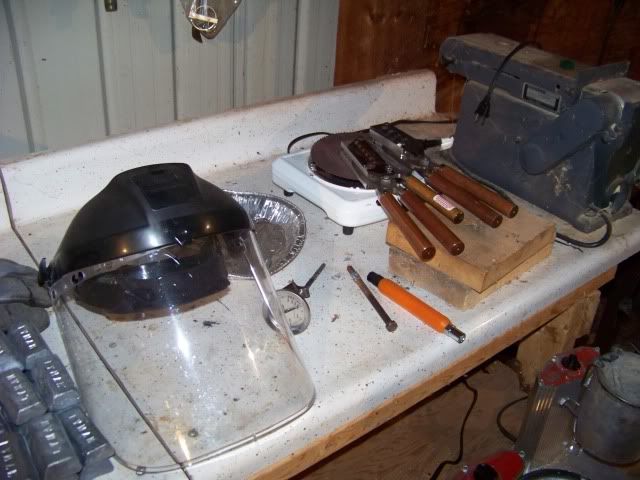
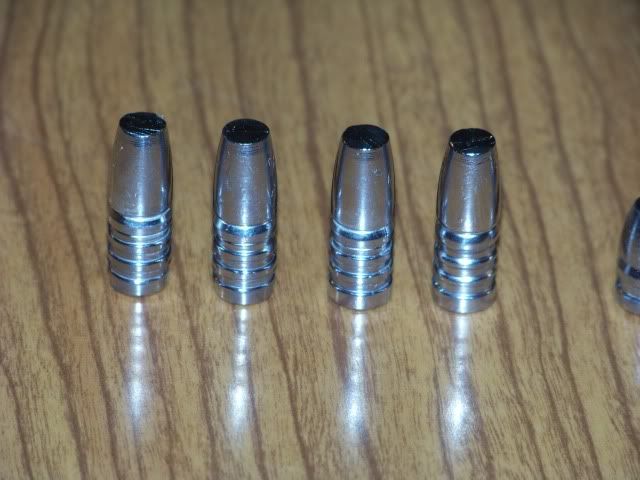