Oliver Sudden
New member
I'm a fairly experienced caster but can not seem to over come getting a void in the base of a mini bullet. Note the dark half moon in the photo. I have two different molds that produce the same flaw. These are pure lead as they should be and the molds have been carefully cleaned and pre heated. I've tried casting from the bottom pore both touching and not, ladle pore, as I do for my Sharps, with different speeds of pores. Fine looking bullets on the out side and even if the base cavity looks good the weight varies as much as 20 grains. Ideas?
IMG_0251 by Oliver Sudden, on Flickr
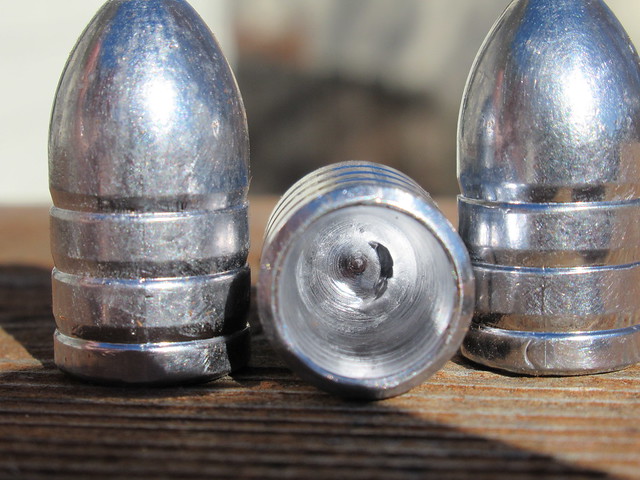