Do your Redding type "S" bushing dies do this to your necks?
Hello everyone , I've been having this issue for quite some time now and thought I'd inform you all what I have found . Although I "kinda know what's going on It's not completely clear as to why It's happening . Feel free to suggest what you think is causing the problem or other ways to fix it . For the most part this thread is a PSA to all that use the Redding type "S: bushing dies .
Now to the problem .
For quite some time now and really ever since I started using the bushing dies . I've been getting Flared or belled necks at the mouth . This does not happen with all lots of brass and appears to happen most with LC brass . Now I use MUCH more LC brass then any other so that may explain why It seems to happen with those only . I still need to test if any other brass does this as much as LC does . Although it is noticeable by the naked eye , It's hard to see at a glance . When you magnify the case and get a closer look it's clear there is a problem .
308 LC-( forget the year ) FL sized using bushing .002 smaller then the loaded OD of the neck WITH OUT expander ball.
5.56 LC-14 FL sized using bushing .003 smaller then the loaded OD of the neck WITH OUT expander ball.
These cases were once fired by military and bought from my local range . As you can see there is a clear belling and or flare at the case mouth which results in very inconsistent bullet hold .
Now if you use the expander ball when sizing the problem goes away .
Pretty crazy right ? yea I was starting to get pretty frustrated because If I have to use the expander to size my cases , Why use the bushing die ?
So I finally contacted Redding as well as talking with a couple experienced reloaders about the problem .
I emailed Redding and informed them of the problem I've been having . Before that I did some measurements and was very surprised as to what I found . I always thought that the case mouth was experiencing spring back that was causing the flare . Turns out the mouth is just about the right diameter as the bushing used but the rest of the neck is actually sized down an extra .004 o .005 then the bushing size .
Meaning : My loaded cartridge necks OD is .337 so I use a .335 bushing . After FL sizing the mouth measures .334 but the center and lower section of the neck measures .331 0r .330 . Wait what ??? the neck or part of it is being sized down .004 smaller the the actual bushing being used ??? Well that's not making any sense right ?????
So I emailed Redding and explained the issue . I'm leaving some of the back and forth out because some was just making sure we understood each other .
Reddings reply :
My response :
I then went on to give him the measurements I had come up with . At the time I was testing the LC-14 5.56 brass . There was some confusion about my measurements between him and I but the final result/reply from Redding was
Now If you use the expander ball it reforms the neck and all works just fine but that defeats the purpose of the bushing die .
The fix so far is to size the neck down in increments . Lets say you want to size the outside diameter of the neck to .245 but your fired case neck measures .254 . You first must size it down with a .250 bushing , then again with the .245 bushing . I can confirm that this does work .
There is another way how ever that seems to work well . You can use a Lee collet neck die to size the neck down first then run the case through the FL bushing die with the proper bushing . That also works and stops the belling of the case mouth .
I how ever found a silver lining in all this . I use a universal de-capping die to deprime all my cases first . I then clean primer pockets and brush inside of necks before first tumble . Instead of using the universal die to de-prime . I de-prime when I do the first neck sizing . For me and my process there is no extra step really just a different one .
I've been holding off on posting anything about this until I had a full picture to provide you all .
What say you ??
Hello everyone , I've been having this issue for quite some time now and thought I'd inform you all what I have found . Although I "kinda know what's going on It's not completely clear as to why It's happening . Feel free to suggest what you think is causing the problem or other ways to fix it . For the most part this thread is a PSA to all that use the Redding type "S: bushing dies .
Now to the problem .
For quite some time now and really ever since I started using the bushing dies . I've been getting Flared or belled necks at the mouth . This does not happen with all lots of brass and appears to happen most with LC brass . Now I use MUCH more LC brass then any other so that may explain why It seems to happen with those only . I still need to test if any other brass does this as much as LC does . Although it is noticeable by the naked eye , It's hard to see at a glance . When you magnify the case and get a closer look it's clear there is a problem .
308 LC-( forget the year ) FL sized using bushing .002 smaller then the loaded OD of the neck WITH OUT expander ball.

5.56 LC-14 FL sized using bushing .003 smaller then the loaded OD of the neck WITH OUT expander ball.
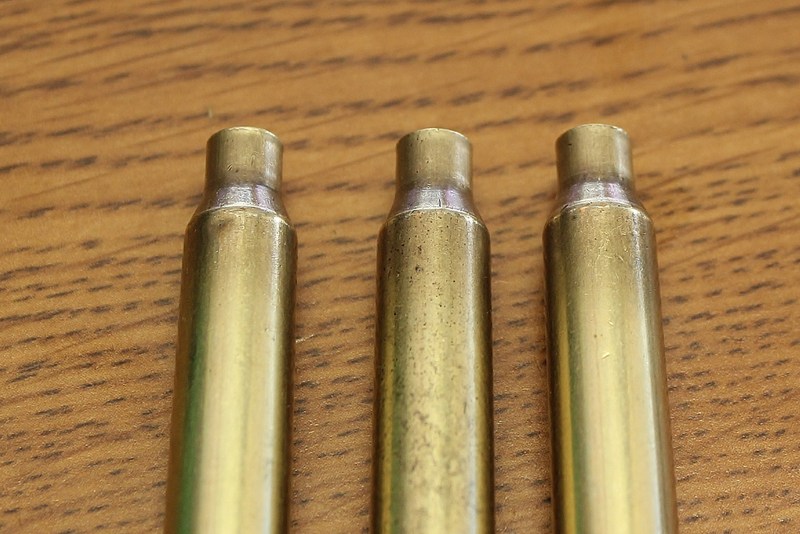
These cases were once fired by military and bought from my local range . As you can see there is a clear belling and or flare at the case mouth which results in very inconsistent bullet hold .
Now if you use the expander ball when sizing the problem goes away .

Pretty crazy right ? yea I was starting to get pretty frustrated because If I have to use the expander to size my cases , Why use the bushing die ?
So I finally contacted Redding as well as talking with a couple experienced reloaders about the problem .
I emailed Redding and informed them of the problem I've been having . Before that I did some measurements and was very surprised as to what I found . I always thought that the case mouth was experiencing spring back that was causing the flare . Turns out the mouth is just about the right diameter as the bushing used but the rest of the neck is actually sized down an extra .004 o .005 then the bushing size .
Meaning : My loaded cartridge necks OD is .337 so I use a .335 bushing . After FL sizing the mouth measures .334 but the center and lower section of the neck measures .331 0r .330 . Wait what ??? the neck or part of it is being sized down .004 smaller the the actual bushing being used ??? Well that's not making any sense right ?????
So I emailed Redding and explained the issue . I'm leaving some of the back and forth out because some was just making sure we understood each other .
Reddings reply :
I have seen this one other time, however it happened with a regular
FL sizing die. Seems the gentlemen's chamber was rather large in the
neck and the die was reducing the case neck down a significant amount
causing the case mouth to flare.
In my experience I have not found LC brass to be consistent with
regards to neck wall thickness.
I do think the problem has to do with the brass itself and may be one
of following.
Inconsistent neck wall thickness.
For instance your 5.56 loaded round that measures .2465 tells me its
neck wall thickness is .01125". Now if you have a sized case having
an ID of .245 using .245 bushing w/out the sizing button, that tells
me its neck wall thickness is .015. That is a difference of .003475"
between the 2 cases.
Reducing the diameter of a fired case down by .008" or more could
create a flare on the case mouth. What does the neck OD of a fired
round measure, for both the 556 & 308? By subtracting the bushing
size from those measurements it will tell us how far down the bushing
is needing to reduce the case mouth.
The thing that is puzzling is that it doesn't happen on every case.
Right?
My response :
I should have been more clear on what cases have the issue and which do not . I buy my brass from my local range where the Navy and coast guard shoot . The range then sells there brass is 250rd lots . When I say not all cases flare . I should have said not all of the lots flare . If one of the cases in a 250ct lot flares then they all do . I have bought those 250ct lots where none of the cases flared . That's what I meant by not all have this issue .
I then went on to give him the measurements I had come up with . At the time I was testing the LC-14 5.56 brass . There was some confusion about my measurements between him and I but the final result/reply from Redding was
It is not uncommon for any one of the brass manufacturers to produce brass within this range from lot to lot or year to year etc. Therefore it is not uncommon for the reloader to have several different bushing sizes on his bench to accommodate different thicknesses. The only way to get around using 1 bushing size would be to turn all case necks to a consistent neck wall thickness. The only other option is to use a standard FL sizing die. You may find for your situation it might be best to use a FL sizing die for the LC brass you purchase and use the B/FL die for Lapua, Nosler or Norma. I have found those three to have some of the best quality as well as most consistent.
With regards to a sized case coming out smaller than the bushing size. The only definitive way to determine if the bushing is in spec would be to have a machine shop pin it. You are also welcome to send the bushing back here where we can check it as well.
I have pasted below a quick explanation of how this can occur.
It has come to our attention through customer calls and our own use of the bushing style sizing dies that in certain instances, a given neck sizing bushing will produce a case neck diameter that can be several thousandths of an inch smaller than the actual diameter of the bushing. This idiosyncrasy occurs when the neck diameter of the fired case is a great deal larger than the diameter of the neck sizing bushing, such as occurs when factory chambers are on the large side of the tolerance range. Typically, we have not noticed any problems until the case neck is reduced more than 0.008-0.010". (your fired case .254 - .245 bushing = .009")
Solutions include, increasing bushing diameter to compensate and/or the use of a size button. Reducing the neck diameter in two smaller steps by using an intermediate diameter bushing will also help. More concentric necks will also result using this method, as the case necks are stressed less during sizing. Don't forget to properly chamfer the inside and outside of the case mouths and apply a light coating of lubricant to the case necks before sizing.
Now If you use the expander ball it reforms the neck and all works just fine but that defeats the purpose of the bushing die .
The fix so far is to size the neck down in increments . Lets say you want to size the outside diameter of the neck to .245 but your fired case neck measures .254 . You first must size it down with a .250 bushing , then again with the .245 bushing . I can confirm that this does work .
There is another way how ever that seems to work well . You can use a Lee collet neck die to size the neck down first then run the case through the FL bushing die with the proper bushing . That also works and stops the belling of the case mouth .
I how ever found a silver lining in all this . I use a universal de-capping die to deprime all my cases first . I then clean primer pockets and brush inside of necks before first tumble . Instead of using the universal die to de-prime . I de-prime when I do the first neck sizing . For me and my process there is no extra step really just a different one .
I've been holding off on posting anything about this until I had a full picture to provide you all .
What say you ??
Last edited: